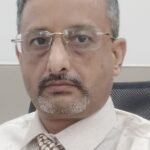
RAVEE PANDE
About Candidate
Negotations & Contracting
Cost Reduection Tools
Strategic Sourcing
On Line Auction
Alternate Sourcing
Spend Analysis & Consolatation
AMC/CMC/ARC/ Long Term Rate Contracts
Logistics & Supply Chain Management
Global Procurement
People Management
Large Capex & Opex – Indirect Spend
ERP Implimentation
Problem Solving
Stake Holder Enguagement
Problem Solving
Location
Education
INTERNATIONAL BUSINESS
PHYSICA CHECMISTRY MATHS
( CERTIFIED PROCUREMENT PROFESSIONAL)
Work & Experience
Function Head of Purchasing Group Strategy and Development • Develop and implement a strategy to ensure the function is operating in line with the objectives of the business to add value, mitigate supply chain risk and deliver cost savings in the time frame. • Create and implement best practice purchasing vision, strategy, policies, processes and procedures to aid and improve business performance. • Ensure that purchasing strategies and processes are in place to meet business objectives and operational needs in terms of price, quality and delivery targets, which enables the company to function and compete effectively in the market • Evaluate the challenges faced by the business and take action to mitigate risks and develop opportunities Procurement Operations Management (Indirect - CAPEX OPEX ) • Overall responsibility for Purchasing and Cost Estimating activities across the business for the sped of Rs 200 Cr for various categories like Equipment, Change Parts, IT ( both Hardware , software , Renewals ), Imports, Lab Chemicals, AMC/CMC/ Rate contract for HO, Plants and R & D , Initiate P2P cycle…. • Ability to negotiate at CxO level., • Prepare and manage the annual Purchasing budget and forecasts as well as ensuring compliance with customer and legal requirements. • Craft negotiation strategies, negotiate contract terms with key suppliers to ensure value for money, quality standards and delivery terms with technical and operational input from stakeholders keeping in view of business “Bottom Line” • Adopt new ways of working, like “On Line Auction”, Digitization, Reduction of cycle time by elimination of redundant process without compromising the business value. Relationship Management • Responsible for managing relationships and negotiating with key suppliers at a senior and strategic level. Seek and partner with reliable vendors and suppliers . • Develop an overall vendor base which creates and sustains a competitive advantage utilising global market exploitation, leveraging spends and leveraging technologies Stake hold engagement. • Motivate and lead the team. Succession Planning as per organization values. Audit & Compliance • Ensure the full compliance and identify the improvement opportunities.
Responsibilities: - Ownership & Management of End-to-End Supply Chain Management for Nashik & Baroda • Identify long term constraints, bottleneck and key materials Improve systems & processes, order management, invoicing & logistics. Monitor issues and perform root-cause analysis fix it with a Centre of Excellence (CoE) Approach. • Monitor and Improve KPI(s) like LIFR, OTD, U2S, DOS, SLOB, IRA, VMI, JIT, DPO and EOQ. • Vendor Selection through of Procurement Processes such as RPP/RFI/RFQ/e-Auction for both CAPEX & OPEX (Indirect Spend) with value engineering and saving opportunities. Negotiating and Contracting. (MRO & MEP Services).Yearly ARC, AMC/CMC, contract to cover 75% Spend under contract. • Project working on 3PL to replace contract labour and deliver to 15% cost reduction. • SAP Implementation and establishing E Auction / e bidding culture. • Monthly MIS / Dashboard/ Yearly Budget, Spend Analysis & Insights … etc.
Key Deliverables: • Site Procurement Lead (SPL) and Category Manager for Site Indirect Spend (OPEX & CAPEX) Managing Entire Spectrum of procurement function like:- Supplies like PPE, OEM Spares, Maintenance-Repairs-Operations (MRO), Mechanical- Electrical-Plumbing (MEP Services), Engineering Purchases Production Consumables, Lab/R&D Chemicals & Consumables Solvents, Intermediates, Speciality Chemicals, Fine Chemicals, Various EHS services, HPLC Columns, USP Standards, AMC / CMC, etc. Multiple Product Line. Buying of equipment’s & Services under CAPEX. High-Value Soft services like Canteen, Housekeeping, Security Services, Employee Transport, Labour Contracts, and various professional services for GSK Pharma, GSK Vaccine plant and Contract Manufacturing Organization (CMO). Approx. Spend Value Rs 45 Cr (USD 6.43 Mn) with the Centre of Excellence (CoE) approach. API Sourcing worth Rs 86 Cr ( USD 12 Mn ) with support to New Product Development (NPD) • Formation and executing Sourcing Strategy for key supplies and services like PPE, Canteen, Technical services, Tail Spend Management, etc. for plant size of ~ 800 Employee. • Delivery of Site Procurement Plan and Savings Targets. • Deliver excellent customer service and maintain a high level of visibility and performance with site stakeholders • Alignment of Production Procurement activities with site priorities • Ownership and Management of departmental Risk Management Process. New Product Development, Art Work Management compressed lead timings. Support timely closure of NCR/CAPA/Site wide Risk Actions. • Perfect alignment with functional partners like Engineering, HR, Production, EHS, QA/R&D, etc. • Played role of Category Manager to manage spend for key categories like MRO/RMO, Engineering Consumables and Services, Production Consumables, PPE, Lab Chemicals and R & D Consumables, HPLC Columns, USP Standards, Soft & Hard Services, Mechanical, Electrical & Plumbing Services (MEP), Professional Services, Freight & Distribution, Corporate Gifting, Printing, Various AMC / CMC for GSK Pharma and GSK Vaccine plant at Nashik. • Implemented ERP systems like BPCS, J D Edwards & SAP training down the line various users. • Developed various "Bolt-on "software/Modules like (1) Excise Accounting System, (2) “Status Label” Printing for RM, PM & Chemicals and (3) Computerized Maintenance Management System (CMMS) Etc. In-Depth understanding of System architecture and processes of MM PO. • Buying of equipment’s for QA Lab & R & D Lab with TCO approach and contracting the Services like Method Development, Validation. Stability Testing etc. and other critical equipment’s and services. Vendor Development & Management • Vendor Selection Through of Procurement Processes such as RFI / RFP / RFQ /On-Line Auctions • Negotiating and Contracting. Ensuring Annual Rate Contract to cover more than 80% spend and SAP Contracting Life-Cycle Management (CLM) • Influence key business and procurement stakeholders and Stake Holder Engagement. • Identification of Value engineering & Savings opportunities • Regular Update to site on various Global Procurement initiatives. • Support key Supplier Relationship Management (SRM) • Support Data Accuracy within site systems. (Supplier Data, Budget & Spend & data. Monthly MIS / Dashboard/ Spend Analysis & Insights). • Usage of Modern techniques like “e- bidding” / “On line Auction” (Forward / Reverse), CAMMS etc. • Tracking the savings generated on Global Platform “Galaxy” Stakeholders’ Management • Managing relationships with over-demanding 20 key Stakeholders across the Site. • Balancing the expectations of both Procurement and site stakeholders with full compliance. • Balancing both strategic and operational requirements. • Crises Management during shortage/rejections of RM/PM Statutory Compliances • Ensuring adherence ABAC and now TPO ( Risk Management Process for Vendors ) • Strict adherence to the Site SOP & Global Procurement Policies. • Faced Audit by SOX, KPMG, PWC, EY, IRA. Ensuring No audit observation/findings. • Support to timely closure of CAPA / NCR, Risk Mitigation Actions and Change Management
IIPMR ( Certified Procurement Professional - CPP Certification ) Roles & Responsibilities: • Purchase – Direct & Indirect Spend | Apr 2008 - Feb 2012 • Purchase - Direct Spend | Oct 2005 - Mar 2008 • Production Planning & Control – PPC | Apr 2004 – Sep 2005 • Raw & Packing Material Stores | Jan 2000 - Mar 2004 • Finished Goods Logistics & Excise | Sep 1996 – Dec 1999 Procurement, Product Planning & Control, and Materials/ Stores Management • Direct Spend and Indirect Spend. • OPEX and CAPEX spend worth ~ Rs 12 Cr and Rs 2 Cr = Rs 14 Cr for Site. • OPEX Spend consists of Maintenance-Repairs-Operations (MRO), Mechanical-Electricals-Plumbing ( MEP Services) Production Consumables, PPE and other EHS requirements, Lab chemicals for QA and R & D, AMC/ CMC. • Various soft services like Canteen, Security, Employee Transport and House Keeping, Method Development, RM testing by third party for classified manufacturing area. • Scrap Sale Contract and Hazardous Waste disposal contract with coordination with stores. • Maintaining the PR to PO release turn-out time as per site SLA. • SOX Audit compliance and KPMG Audit as per schedule. • Identifying various new saving opportunities and Non-PPV monitoring and achieving target. • Usage of "On-Line Auction” tool. • Monthly MIS / Dash Board and Governance. • Procurement of RM / PM and Budget setting exercise • Purchase audit facing audits like SOX and audit like PWC and KPMG. • Vendor development and management • Generation of Weekly plan based on “on hand “ and “In-transit” stock for mother plant & contract manufacturing • KPI Strike Rate of 95% by number of batches and 98% by Value. Utilization of Optimization of production capacity for both locations. • Monitoring of receipt of Needles (Basic raw material) and planning the schedule. • Monitoring the daily production schedule and its update the same to Site Director and Crises management. • Deeply involved in materials/ store management related to Raw & Packing Material. Logistics Management • End to End organizing and monitoring Receipts (Domestic and Imported FG), storage and distribution of goods. • Contract formation with Transporter and Packing agency. • Managing the Freight Budget and meeting delivery Lead Times. • Keep track of quality, quantity, stock levels, delivery times, transport costs and efficiency. • Invoicing and Distribution of Finished Goods of ~ 1500 SKU from plant to various 225 dealer(s) across India. Export to South Asian Countries. • Manage the entire order cycle to enhance business development and ensure sustainability and customer satisfaction. • Strategically plan and manage logistics, warehouse, transportation and customer services. Error-free Shipments. Resolve any arising problems or Customer Complaints. • Maintaining Inventory Record Accuracy (IRA) above 98% as per a KPI. • Disposal of Hazardous & Non-Hazardous Waste Disposal (Scrap) as per regulatory requirements. • Maintaining the records like RG1 as per Central Excise requirement. • Support for various Excise Audits.